As Reliability Engineering and Condition Monitoring based company that has been established since 1995, PT. Tiara Vibrasindo Pratama always try to innovate and facilitate reliability engineering and condition monitoring practitioners in Indonesia. Thus, we created this place and facility for all reliability practitioners to share Best Practice that has been done by each companies. Best Practice is a process, procedure and execution that has been proved as solutions. This place is more well-known as Tiara Reliability User Conference (TRUC).
TRUC 2018 was held on 31st July – 2nd August in Tanjung Benoa, Bali. This year’s theme was Achieving Tangible Reliability Through Optimization of Life Cycle Strategy Execution. This was formed with the importance of reliability activity planning for equipment throughout its life cycle stage. This article will describe the summary of Best Practice formulation for Asset Maintenance.
Best Practice Formulation for Asset Maintenance – Reliability Availability Maintainability Analysis
Reliability, Availability & Maintainability (RAM) Background
RAM Analysis (Reliability, Availability & Maintainability) is an analysis that describes operation time (reliability) and maintenance time (maintainability) for equipment. Meanwhile, availability is a comparison value between operation equipment time with total operation time and maintenance equipment time. Other description for reliability is Time to Failure, and Time to Repair is other description of maintainability.
The calculation of parameter value on RAM Analysis should be done on an equipment level, even on more detailed stage failure mode. Analysis for equipment could help us identifying bad actors on plant or factory. If the identify process was done on failure mode stage, the collected data could also help identifies the effectiveness of a maintenance strategy.
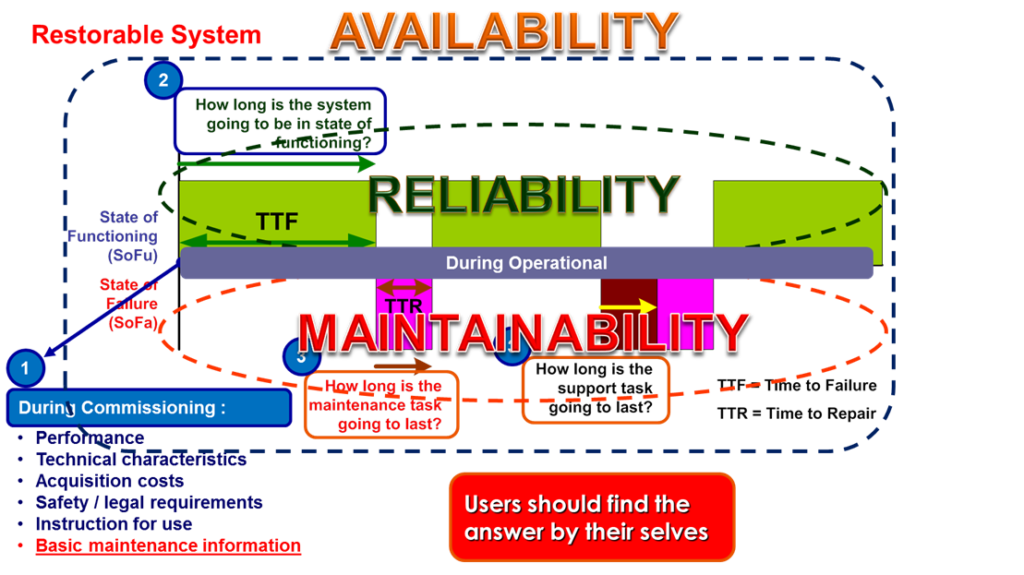
Picture 1. Reliability, Availability & Maintainability (RAM) Graphic
There are so many equipment in one plant or factory that reliability engineer will find it quite hard to decide which equipment that the maintenance strategy should be first evaluated. One of the most helpful method is to register critical damaged equipment. Other method is by defining Mean Time Between Failure (MTBF) and Mean Time to Repair (MTTR) data. This RAM analysis could help Reliability Engineer to get that needed information. Data preparation starts with identifying when will one equipment shuts down and defining the needed time to repair that equipment. Thus, RAM Analysis helps MTTF and MTTR evaluation.
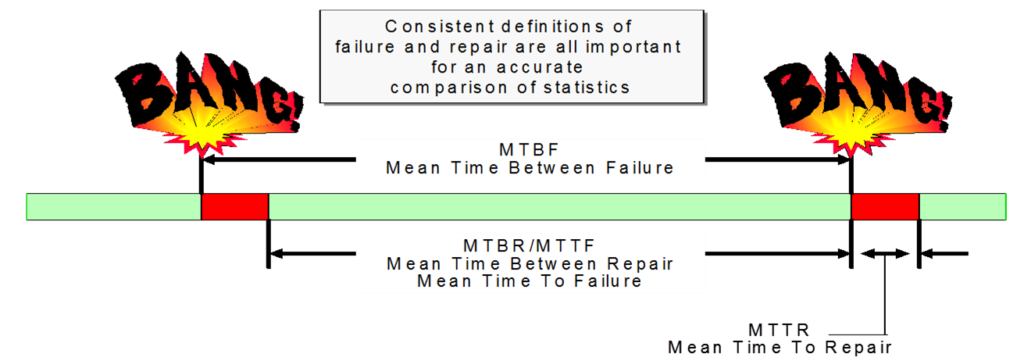
Picture 2. Mean Time between Failure (MTBF), Mean Time to Repair (MTTR) & Mean Time to Failure (MTTF)
For more comprehensive analysis on a factory, RAM analysis should be associated with Reliability Black Diagram (RBD) Analysis. RBD Analysis is a RAM method which could further evaluates a configuration system of optimum Factory Availability development.
Scientifically, reliability parameter is measured with percentage. Weibull equation method is usually used for the measurement. On manufacture industries, deriving Weibull-Reliability curve (Picture 3) is concluded by testing factory equipment until its failure. For examples there are 1000 equipment to be tested, and that equipment are still 100% working perfectly. If along the process there are some equipment failure (reliability becomes less than 100%) and all those failure time gaps between one equipment to another should be recorded and calculated, until there is no more equipment to be tested (0% reliability).
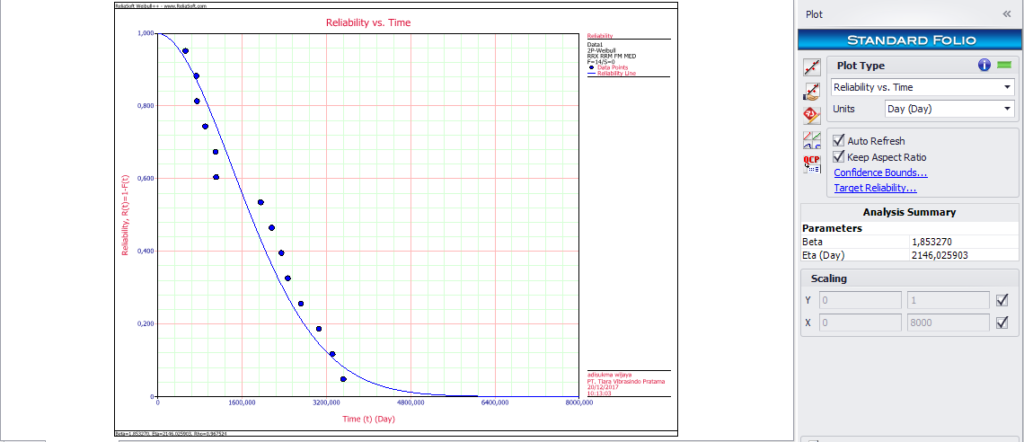
Picture 3. Weibull Curve
The purpose of RAM analysis is:
- Evaluation and development of reliability equipment. Evaluation specifically could be done by defining failed equipment, what kind of failure mode that often come up and what development should be done.
- Evaluation and development equipment’s maintainability. Evaluation start from defining Mean Time to Repair (MTTR) for each equipment. So we could define factors that needs to be develop such as; competency, tools planning and material planning.
Scope of Work
- Data processing is started by defining equipment failure time, which come from Work Order or Maintenance Order and Factory Shutdown report. The data should obtain MTTF and MTTF. Data processing should be on equipment level or more specifically on failure mode level for each equipment.
Equipment failure time data is also used on Reliability data with Weibull method, so those data show Weibull parameters that is needed for RBD process.
- Data processing strings up equipment to become one working factory in RBD process. Equipment string is observed from the field or Technical Graphic (P&ID and PFD). Each equipment is being strung together with one another to build one factory system.
- The implementation is prioritized with critical tools to define failure mode
- This analysis could trigger RCFA on equipment that are sensitive to failure.
Opportunity
RAM analysis utilization:
- CMMS application as maintenance implementation data source and historical data
- Work order or maintenance work development on CMMS
- Factory shutdown report or equipment that is used to record factory activities.
Obstacles
RAM Analysis obstacles:
- Ununiformed failure code. If failure code in uniform, RAM analysis could be done automatically. This advantage could be used for Reliability Engineer to develop FMEA and RCFA activities.
- Inconsistent feedback on work duration from executors. Work duration will describe the needed time to finish a job. Consistent MTTR data will help to increase executors’ productivity to do their job.
- Accuracy input process for failure mode information. Inaccuracy will make Reliability Engineer repeat the work to review and to register the correct equipment.
- Uneven distribution of data processing competency. Data analysis should have its own special training. Record every failure on every equipment on certain amount of time is one of the things to improve data processing competence. And then, engineer could analyze failure mode on every failure that happens.
Work Method
On doing RAM analysis, several methods are needed so the whole process could be done perfectly, such as completed tools or technologies, business process and competence.
Tool/Technology
- CMMS as recording data source. Main data such as: Work Order (WO)/Maintenance Order, WO development time, WO settlement time, Starting Time for Work, and Work Completed Time.
- MS Excel as one of the alternative software to analyze reliability/ maintainability/ availability parameter
Business Process
- PIC to make sure failure code, work duration and actual feedback consistently
- MTBF and MTTR calculation (per failure mode) for each equipment by reliability engineer
- Transaction: justification on equipment with high failure rate and failure mode based on MTBF and MTTR calculation evaluation by reliability engineer.
Competency
- PIC that inputs failure code should have CMMS usage competency and fully understand business process model
- Reliability engineer capable of identify actual failure mode for every WO
For Bahasa Version, please download below: